【摘要】:中空型材挤出机头的典型结构如图4-24所示,长圆柱流道起稳流作用的中空型材挤出机头如图4-25所示。对于简单的异型材机头,也可以将预成型板与口模板合为一块板。a.选择异型材横截面的重心作为挤出中心。这种机头没有死角停滞现象,对敞口式异型材也可采用无型芯和无支架结构。
(1)板式组合机头Ⅰ板式叠加式机头是由几块钢板经加工后组合为一起的机头。这种机头结构,各个钢板零件加工较容易,模具组装简易方便,但每个零件的加工和装配时,必须保证每块模板组装后其中心线要在同一个轴心线上,每个钢板零件间接触处的过渡面要平滑,无滞料死角。如果有过渡死角,要用打磨头打磨成流线型。图4-22所示是较复杂的叠板式挤出机头结构,每块板组合用定位销定位。机头内部的流道可分四段,支架板有两块,后支架板连接分流锥,前支架板安装型芯板。从连接法兰到分流锥构成进料段,两块支架板构成稳流段,压缩板型腔与型芯板构成压缩段,口模板与型芯板的平直段构成定型段。整个流道由这四部分组成,中间的压缩段给定型段形成压力,使型坯密实,整个流道呈平滑过渡。
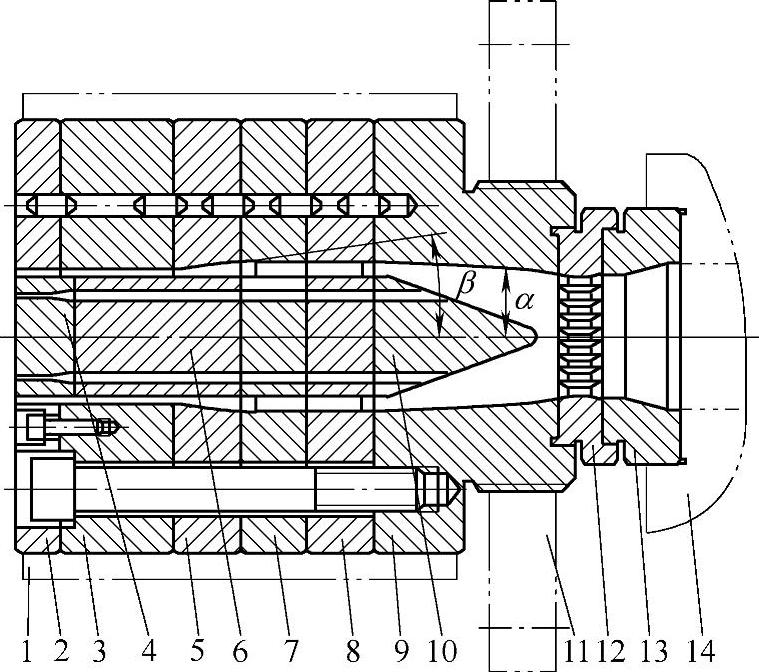
图4-22 叠板式挤出机头结构
1—加热板 2—成型板 3—预成型板 4—镶件 5—压缩板 6—型芯 7、8—支架板 9—机颈 10—分流锥 11—模具法兰 12—多孔板 13—定位套 14—挤出机
图4-23所示的板式组合机头,也是叠加式结构,它用于挤出成型窗框,它的构成和流道结构与图4-22所示的机头基本相同。
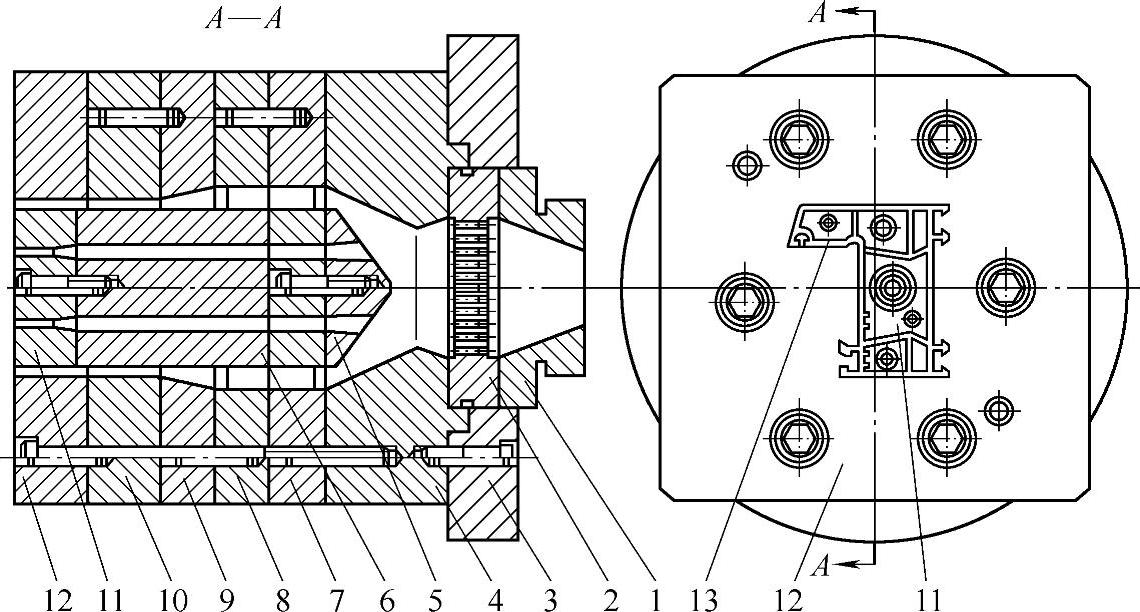
图4-23 窗框机头内部结构
1—过渡套 2—多孔板 3—法兰 4—机颈 5—分流锥 6—型芯 7—支架板(一) 8—支架板(二) 9—收缩板 10—预成型板 11—型芯镶件 12—口模板 13—口模图形
(2)板式组合机头Ⅱ多板式机头加工制造简单,组装方便,整个流道是多块板分段组合连接而成,各模块用定位销和紧固螺栓进行定位和紧固,最终形成一个完整的挤出机头。中空型材挤出机头的典型结构如图4-24所示,长圆柱流道起稳流作用的中空型材挤出机头如图4-25所示。
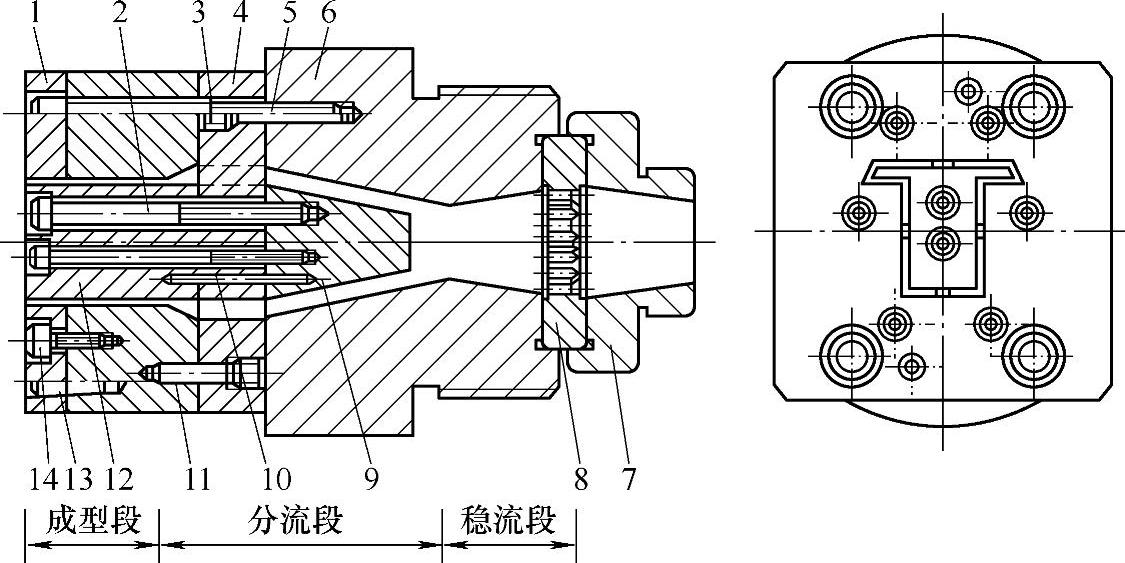
图4-24 中空型材挤出机头典型结构
1—口模板 2、14—螺栓 3—螺塞 4—分流支架 5、10、13—销钉 6—机颈 7—过渡套 8—多孔板 9—分流锥 11—模腔 12—型芯
机头模板的厚度主要根据加工制造的方便程度和流道长度的需要而定。挤出机头的稳流段由多孔板和机颈前半段组成,如图4-24所示。有时也将前半段和后半段分别设计成机颈和机颈过渡板两块模板。图4-25所示是不使用多孔板,而将机颈前半段流道设计成长圆柱形,起稳流作用。
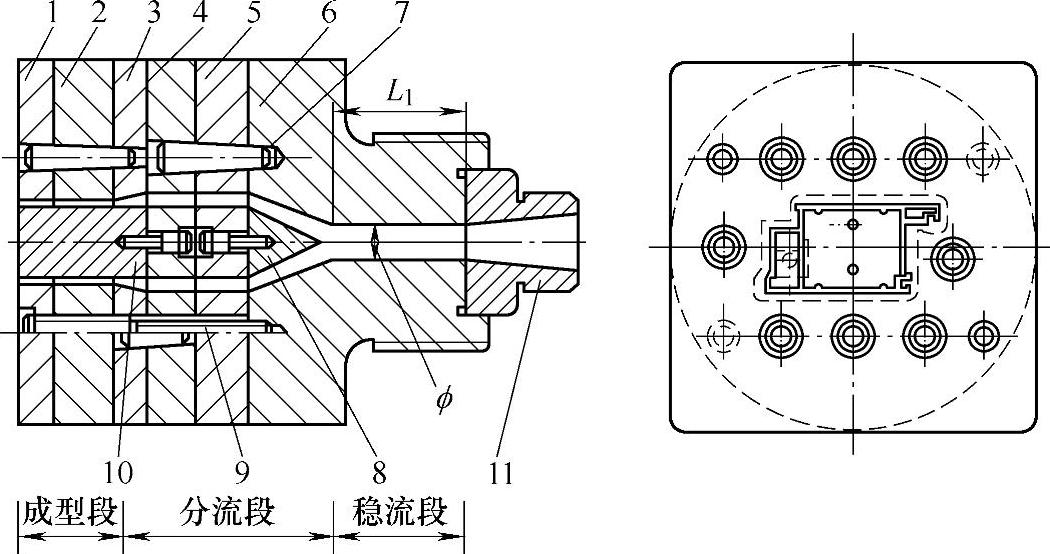
图4-25 长圆柱流道起稳流作用的中空型材挤出机头
1—口模板 2—预成型板 3—收缩板 4—支架板(二) 5—支架板(一) 6—机颈 7—销钉 8—分流锥 9—螺栓 10—型芯 11—过渡套
①挤出机头的分流段从机颈的后半段开始,包括分流锥、分流支架板和收缩(压缩)板。收缩板可以不单独分割成一块模板,而与预成型板组成一块模板,如图4-24所示。开式型材和半开式型材的挤出机头,没有分流锥,也没有分流支架板,如图4-26所示。
②挤出机头的成型段涉及的模板有模腔板(又称预成型板)、口模板(又称成型板)和型芯(又称模芯,开式没有模芯)。对于简单的异型材机头,也可以将预成型板与口模板合为一块板。
③挤出中心选择。异型材挤出中心的选择如图4-27所示。
a.选择异型材横截面的重心作为挤出中心。这样有利于熔体质量流的均匀分流,如图4-27a所示。
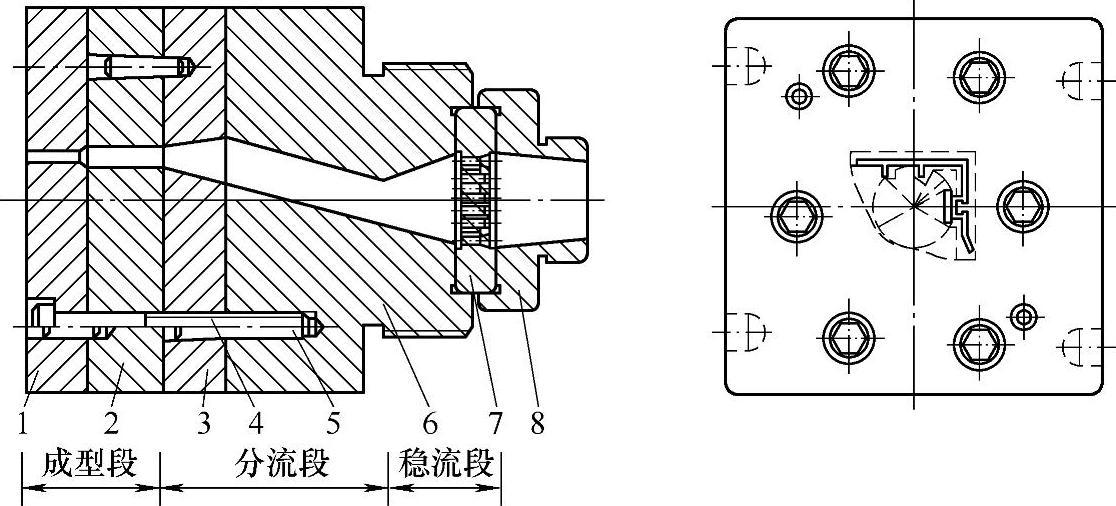
图4-26 开式型材挤出机头
1—口模板 2—预成型板 3—收缩板 4—螺栓 5—销钉 6—机颈 7—多孔板 8—过渡套
b.选择异型材横截面外形的中心作为挤出中心,可以达到让熔体分流路径上的压力损失均衡,如图4-27b所示。对横截面形状较为分散的异型材,这样选择有利于整个机头流道实现均衡地分流,对提高机头的出料稳定性有较大好处,如图4-27c所示。
c.也可选择异型材横截面的主要型腔中心为挤出中心,如图4-27d和图4-27e所示。这样选择有利于对异型材主要部分实现均衡分流,而对个别凸出的部分,在流道上作特别处理,实现整个出胶流道平衡。
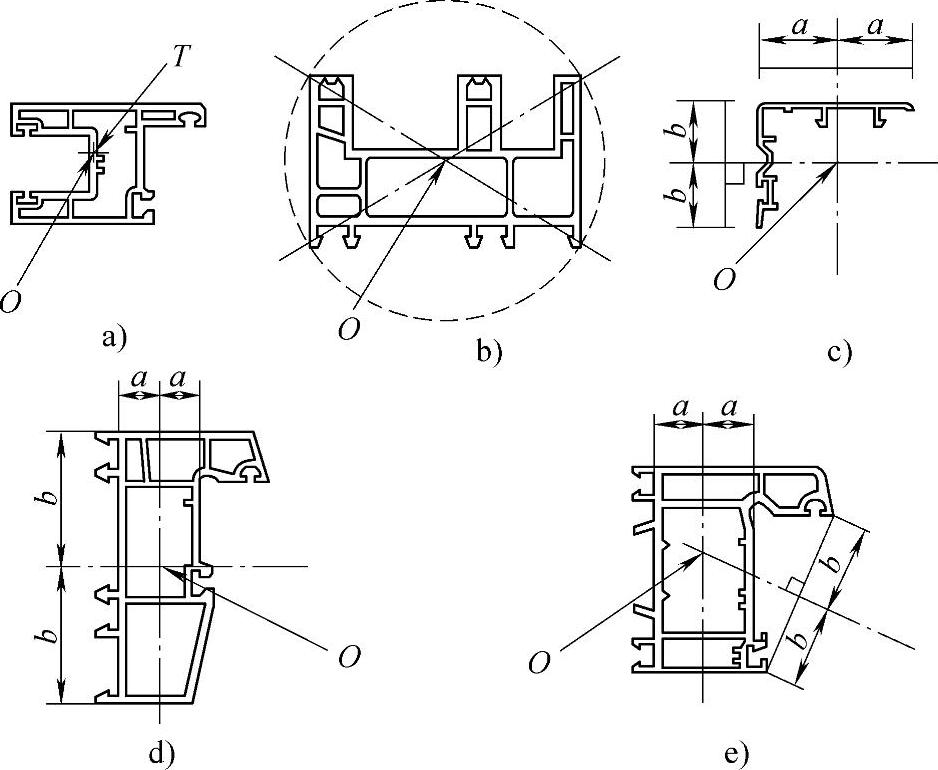
图4-27 异型材挤出中心的选择
T—型材重心 O—型材挤出中心
(3)内腔流线型机头设计 内腔为流线型机头是指熔料流道空腔为流线型,整个变形流线是在一块模板上加工完成的,如图4-28所示。这种机头熔料流道面光滑,无滞料现象,没有板式模块组合时的接触过渡面死角。但这种流线型曲线的加工难度很大,一般要在数控机床或电火花机床上加工,增加了模具加工成本。这种机头没有死角停滞现象,对敞口式异型材也可采用无型芯和无支架结构。流道的长度:进料段等于定型段的2倍,压缩段等于定型段的2~3倍。压缩比为3~7倍口模间隙,最佳压缩角为30°,扩张角<80°。口模定型段长度见表4-5。
(4)内筋和功能块结构设计 在机头设计时,由于模具型腔内还夹有功能块和内筋,要使熔料能平稳均匀地挤出,流道设计要以先分后合为设计原则,这样才能使这些不同形状、不同厚度的功能块、内筋、外壁组成的流道不会相互干扰、串胶,并把这些不同类型的流道在出口定型段汇合,以达到模唇出料均匀性好、流动稳定性强、机头压降低、熔料塑化好、停留时间短、弹性应变残余少的最佳状态。如图4-29所示,相对于型材主体流道而言,直至接近口模出口,内筋的内流道是不与其相通的独立流道。当离出口的距离为k1时,它才与型材主体流道相连。
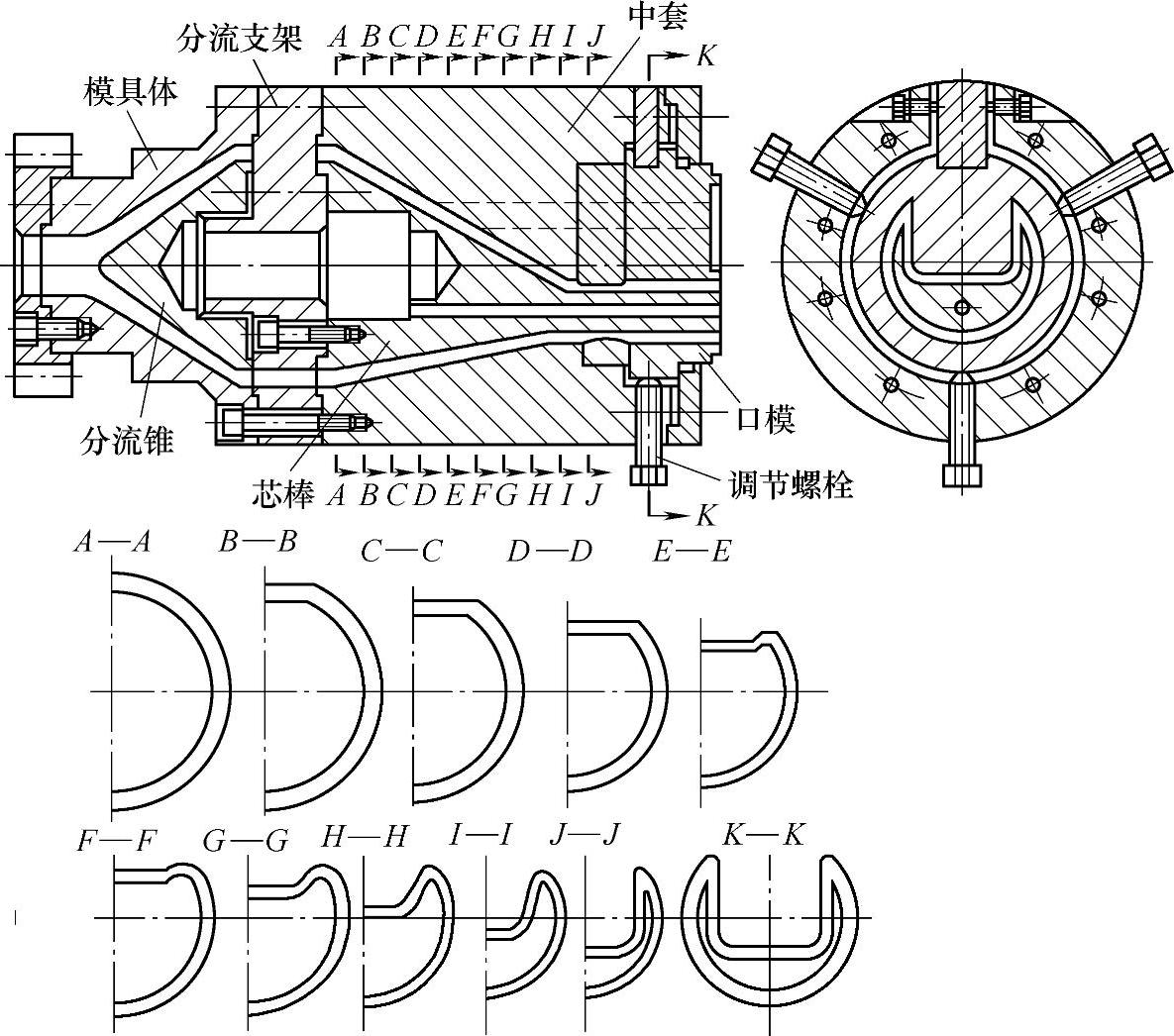
图4-28 内腔流线型机头
支承筋a在流道的一侧,而在支承盘的另一侧加工出平直流道与外壁流道连通,这种内筋外流道如图4-30所示。由于这种流道的料流完全依靠分流支架之后的外壁流道的料流的横向流动生成,很难控制,所以一般只用于10mm以下内筋的流道设计。
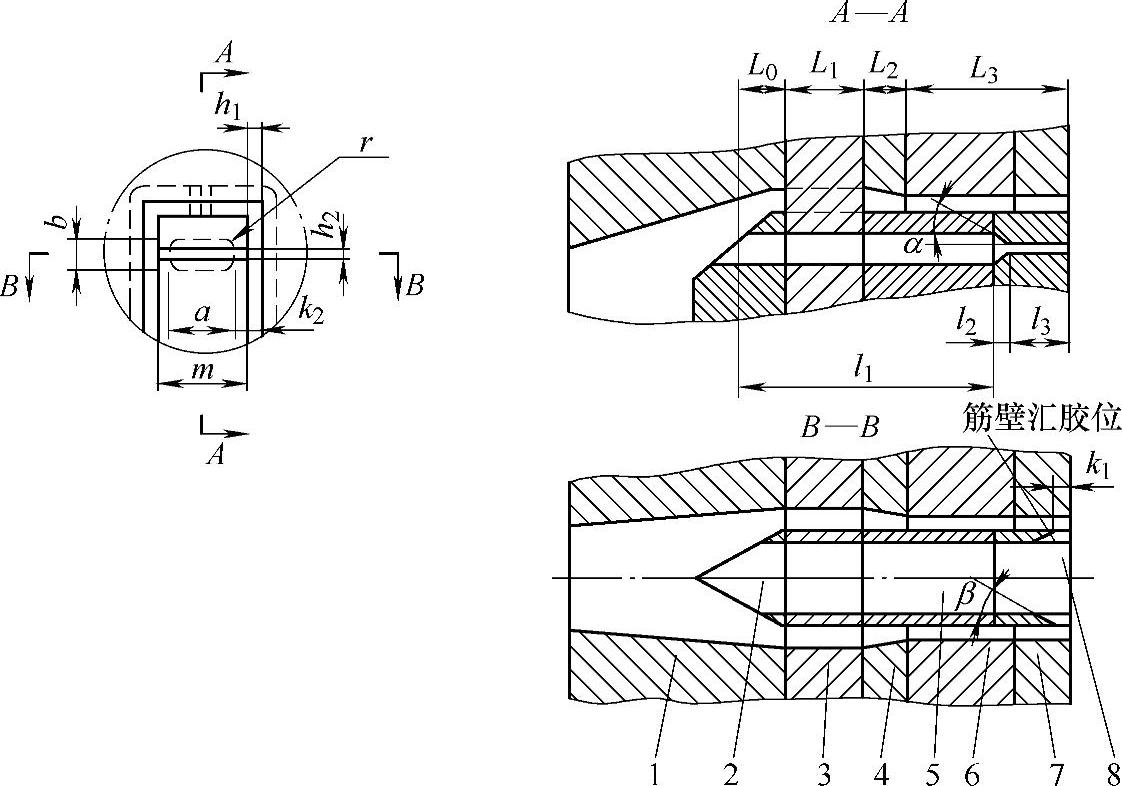
图4-29 内筋的内流道设计
1—机颈 2—分流锥 3—支架板 4—收缩板 5—型芯 6—预成型板 7—口模板 8—型芯镶件
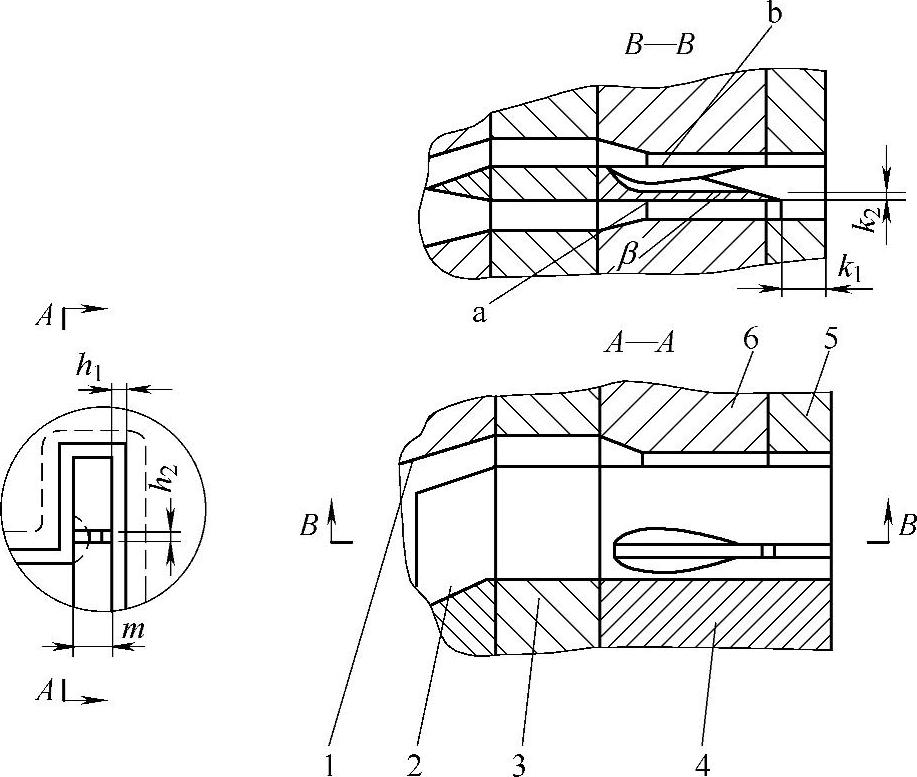
图4-30 型芯一侧与外壁流道连通的内筋外流道
1—机颈 2—分流锥 3—支架板 4—型芯 5—口模板 6—预成型板 a—支撑筋 b—料池
图4-31所示为在内盘型芯上的两侧与外壁流道连通的内筋外流道。
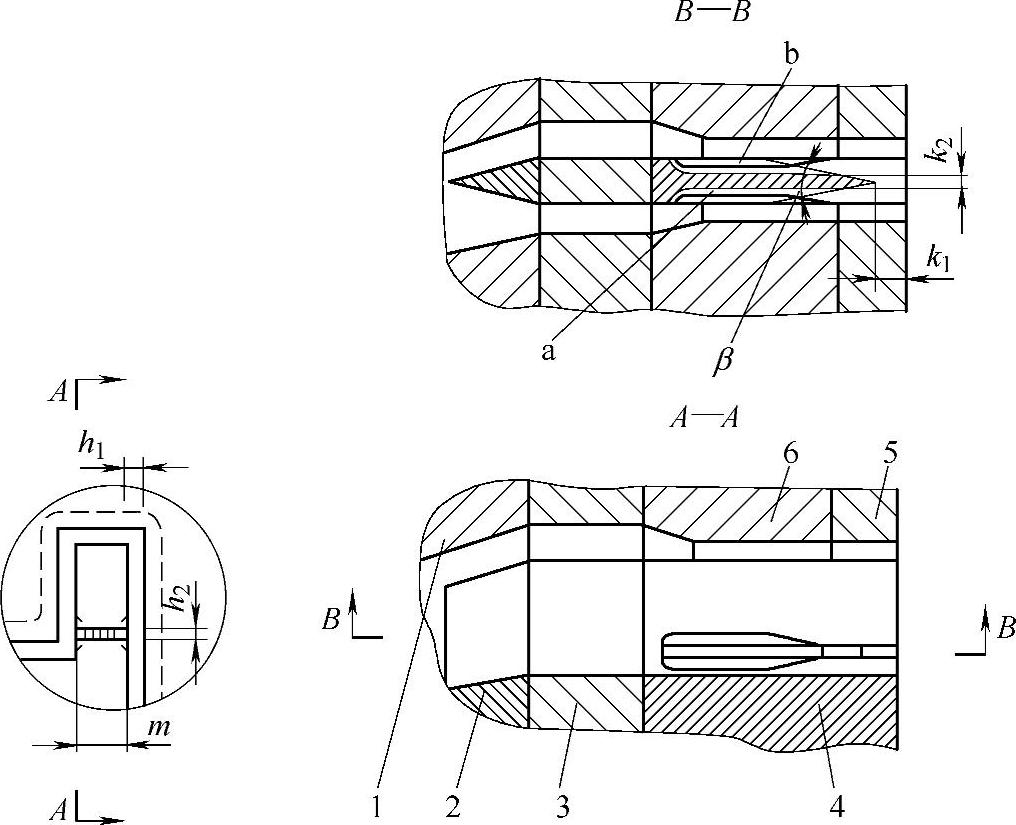
图4-31 型芯上两侧与外壁流道连通的内筋外流道
1—机颈 2—分流锥 3—支架板 4—型芯 5—口模板 6—预成型板 a—支撑筋 b—料池
小凸筋功能块流道设计如图4-32所示。
较大凸筋功能块流道设计如图4-33所示。
一般从机颈开始就将功能块流道与外壁流道完全分开来,设计成相互独立的流道,如图4-34所示。这种流道可不受外壁和其他功能块流道的干扰能独立调节,最终实现在机头出口处(一般在距离口模出胶4~6mm处合流)与外壁一致的平均流速。
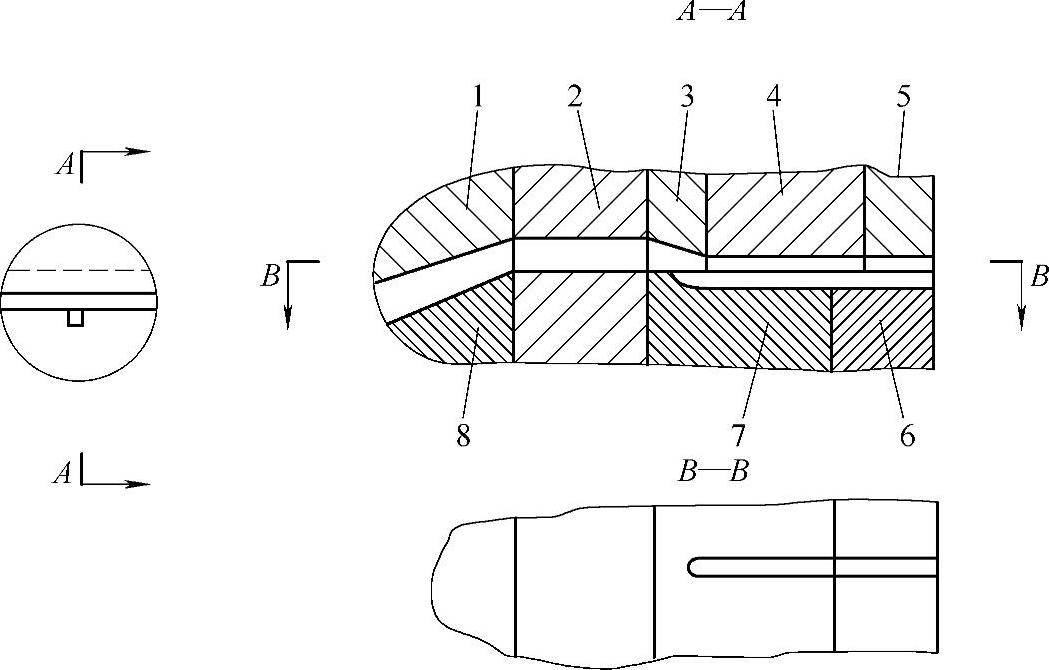
图4-32 小凸筋功能块流道设计
1—机颈 2—支架板 3—收缩板 4—预成型板 5—口模板 6—型芯镶件 7—型芯 8—分流锥
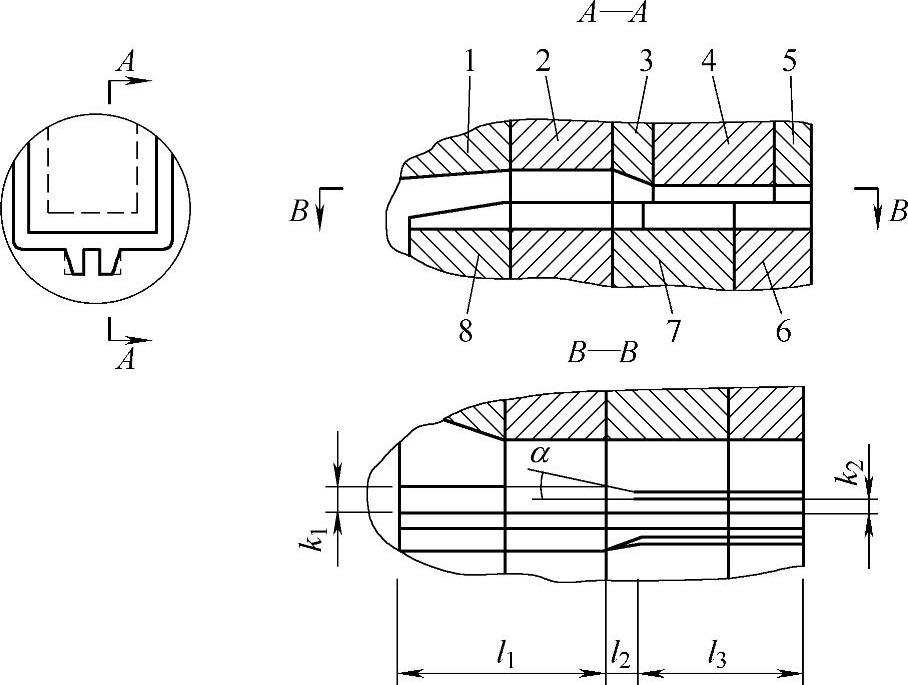
图4-33 较大凸筋功能块流道设计
1—机颈 2—支架板 3—收缩板 4—预成型板 5—口模板 6—型芯镶件 7—型芯 8—分流锥
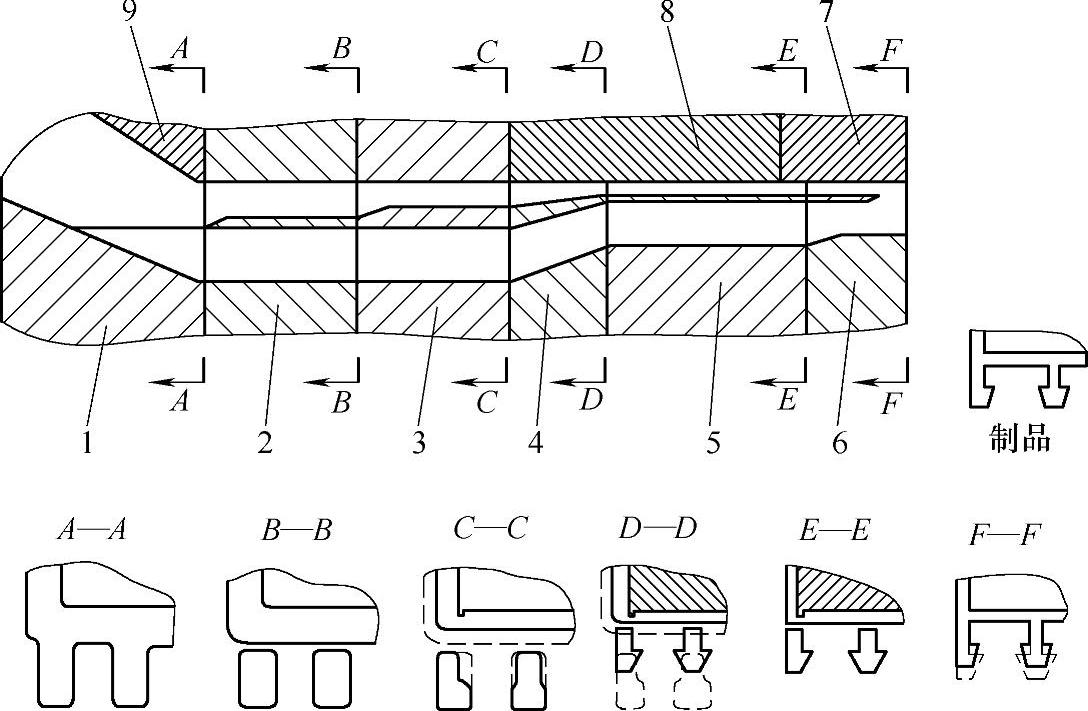
图4-34 完全独立的功能块流道设计
1—机颈 2—支架板(一) 3—支架板(二) 4—收缩板 5—预成型板 6—口模板 7—型芯镶件 8—型芯 9—分流锥
型芯和分流锥的固定方式如图4-35所示,有单板螺栓固定、锥芯一体化设计、两块分流支架板分别用螺栓和销钉固定型芯和分流锥、型芯板和分流支架板与分流锥和支架板组合一起整体加工等多种固定方式。
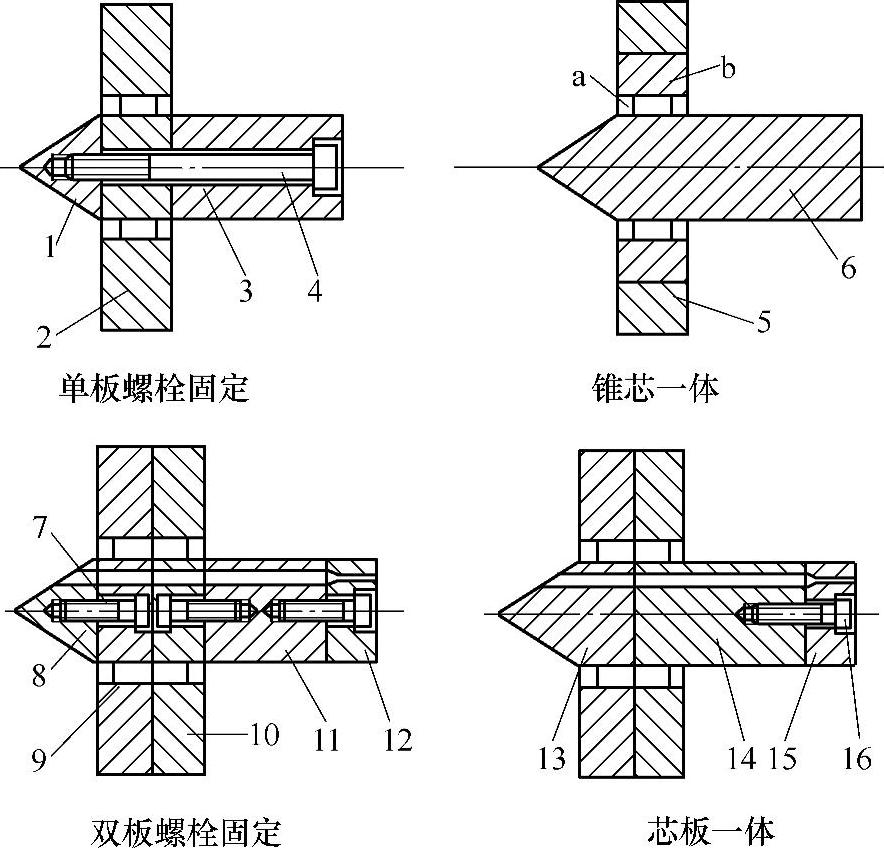
图4-35 型芯和分流锥在分流支架板上的固定方式
1、8—分流锥 2、5—支架板 3、11—型芯 4、7、16—固定螺栓 6—锥芯一体件 9—支架板(一) 10—支架板(二) 12、15—型芯镶件 13—锥板一体件 14—芯板一体件 a—分流筋 b—镶键
相关推荐