【摘要】:减小大型齿轮渗碳淬火畸变的措施1)预备热处理。对于大型齿轮和齿轮轴,采用正火作为预备热处理;对于齿圈,则采用调质处理。
大型齿轮渗碳层深度一般要求3~5mm,最深可达8mm,单件齿轮质量从数吨到数十吨。相应渗碳周期达数十小时,最大可达150~200h。深层渗碳工艺的关键是既要快速渗碳以尽量缩短工艺周期又要限制渗层碳含量过高,以避免不良碳化物的形成及过多残留奥氏体的产生,并减少畸变。
1.大型重载齿轮深层渗碳热处理技术要求
为了防止大型重载齿轮表面硬化层被压碎并防止齿面剥落,其主要热处理技术要求见表5-61。
表5-61 大型重载齿轮深层渗碳热处理技术要求
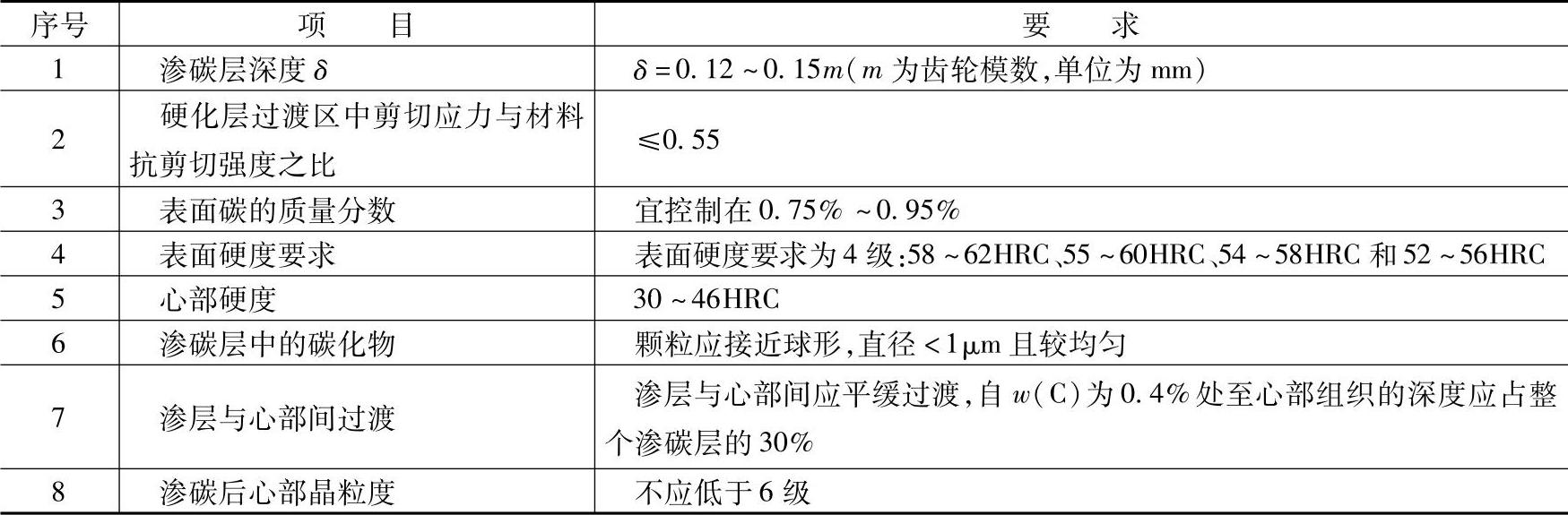
2.大型重载齿轮对渗碳层质量要求和表面碳质量分数及碳化物、残留奥氏体的控制
大型重载齿轮对渗碳层质量要求和表面碳质量分数及碳化物、残留奥氏体的控制见表5-62
表5-62 大型重载齿轮对渗碳层质量要求和表面碳质量分数及碳化物、残留奥氏体的控制
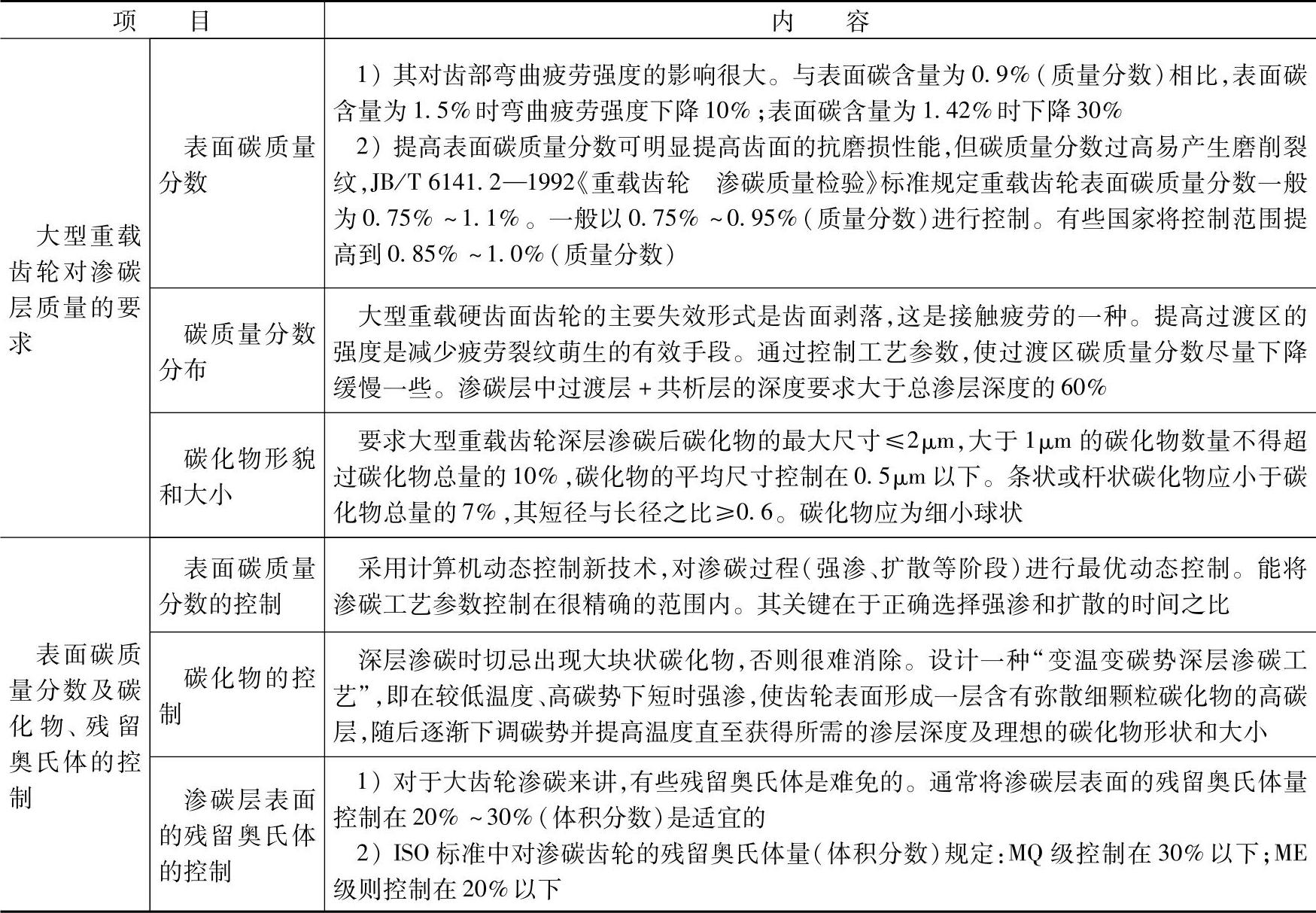
3.大型重载齿轮的深层渗碳工艺
(1)渗碳工艺参数的选择
1)渗碳温度通常选择920~930℃。
2)渗层深度与渗碳扩散时间的关系如下式
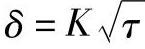
式中 δ——渗碳层深度(mm);
τ——渗碳扩散时间(h);
K——计算系数,根据生产经验确定。据介绍在925℃渗碳扩散时,K值可取0.63;930℃
时,K=0.648;950℃时,K=0.727。
3)强渗与扩散时间的选择。其是根据强渗碳势Cp来确定,在变温变碳势深层渗碳时碳势w(C)1.6%~1.8%,强渗时间(τ1)∶扩散时间(τ2)=1∶4。
大型重载齿轮表面碳的质量分数为0.75%~0.95%。大型重载齿轮表面碳含量控制在下限有利于控制碳化物大小和形状。
(2)典型大型重载齿轮深层渗碳工艺、球化退火工艺及淬火回火工艺 20CrNi2Mo钢大型人字齿轮深层渗碳工艺、球化退火工艺及淬火回火工艺如图5-7所示。
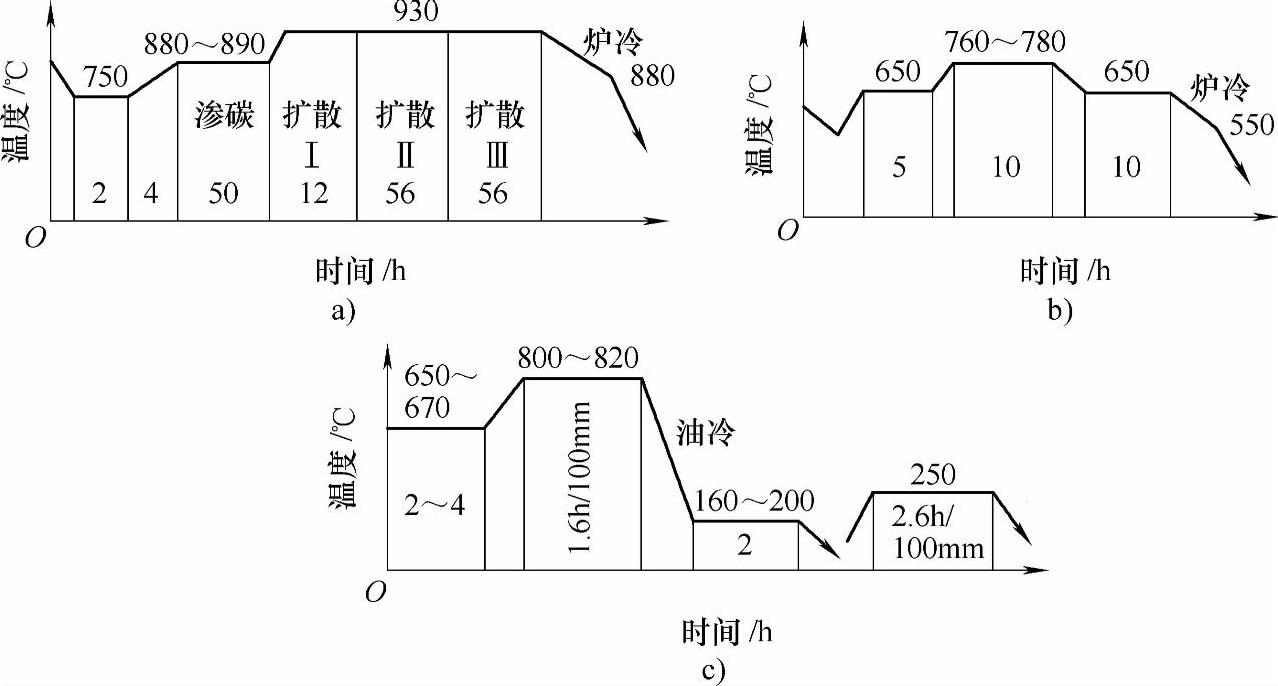
图5-7 20CrNi2Mo钢大型人字齿轮深层渗碳工艺、球化退火工艺及淬火回火工艺
a)变温度变碳势深层渗碳工艺曲线 b)球化退火工艺曲线 c)淬火回火工艺曲线
1)变温度变碳势深层渗碳工艺。均温750℃×2h→渗碳(880~890)℃×4h→强渗(880~890)℃×50h→扩散Ⅰ(从880~890℃升温至930℃并进行保温)×12h→扩散Ⅱ930℃×56h→扩散Ⅲ930℃×56h→炉冷至800℃出炉空冷,如图5-7a所示。
2)球化退火工艺。650℃×5h→(760~780)℃×10h→650℃×10h→炉冷至550℃出炉空冷如图5-7b所示。
3)淬火回火工艺。在保护气氛下预热(650~670)℃×(2~4)h→加热(800~820)℃×1.6h mm→油冷至(160~200)℃×2h→回火250℃×2.6h/mm,如图5-7c所示。
4)检验结果。经渗碳、球化退火、淬火、回火处理后,齿轮有效硬化层深度为6mm,齿面硬度为75~77HS。
(3)减小大型齿轮渗碳淬火畸变的措施
1)预备热处理。对于大型齿轮和齿轮轴,采用正火作为预备热处理;对于齿圈,则采用调质处理。
2)淬火冷却控制。合金钢渗碳后表面马氏体转变温度为130~140℃,将最终冷却温度控制在160~180℃为宜。将油淬齿轮冷至一段时间后,转入180℃炉中回火,保温数小时后,再冷至室温。也可采用80~100℃热油淬火,最终温度120~150℃。
为了防止齿轮和齿圈淬火后产生喇叭状畸变,可用冷端部加盖板的方法改善冷却条件和畸变。为了减小大型齿轮淬火后外圈胀大,可采用将中心孔和轮辐进行预包装封闭的淬火方法。根据齿轮畸变的规律对齿轮的几何尺寸进行预修正,以使最后的磨削量减少到最低程度。
4.大型齿轮渗碳热处理的实例
大型齿轮渗碳热处理的实例见表5-63。
表5-63 大型齿轮渗碳热处理的实例
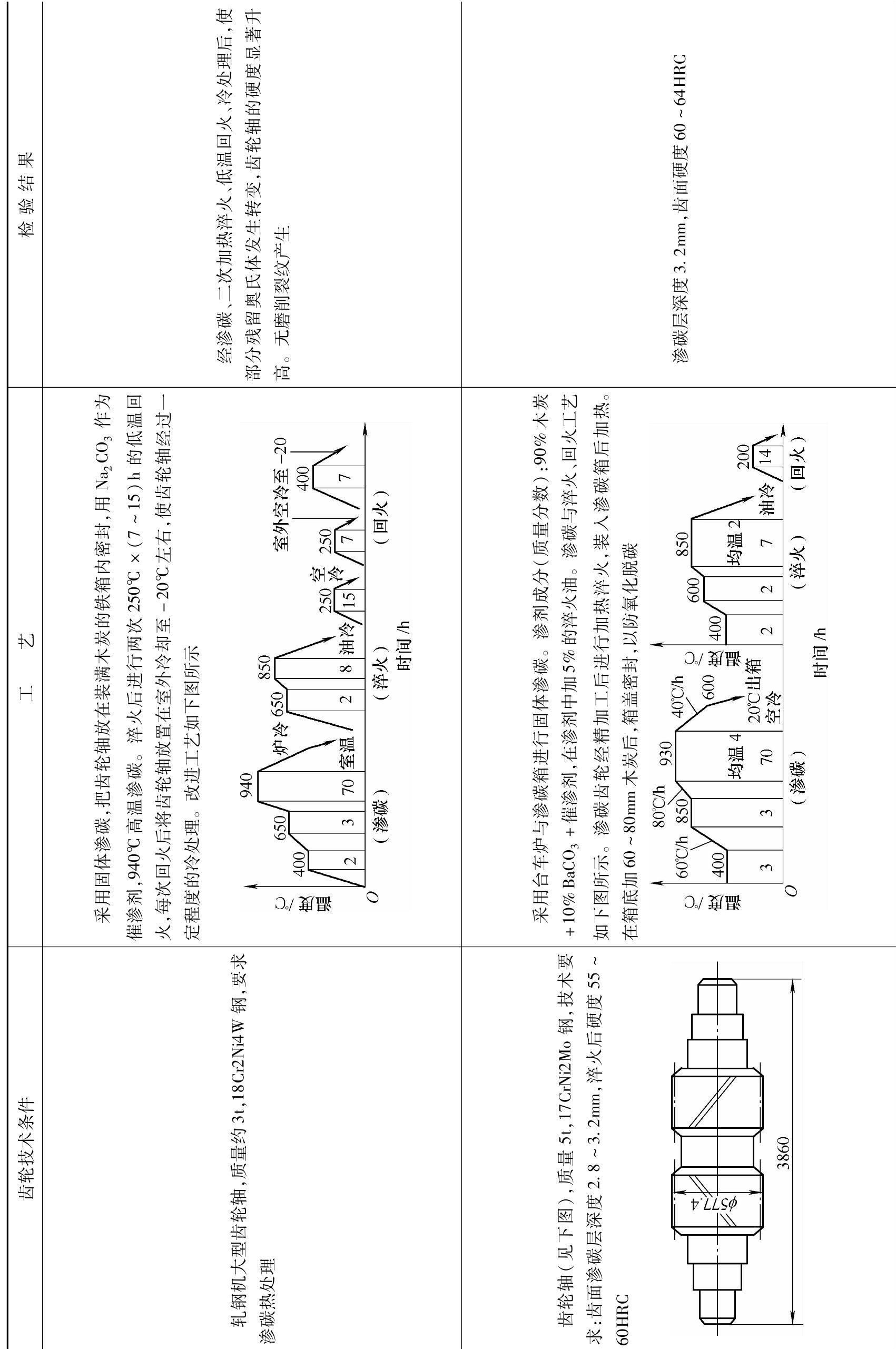
(续)
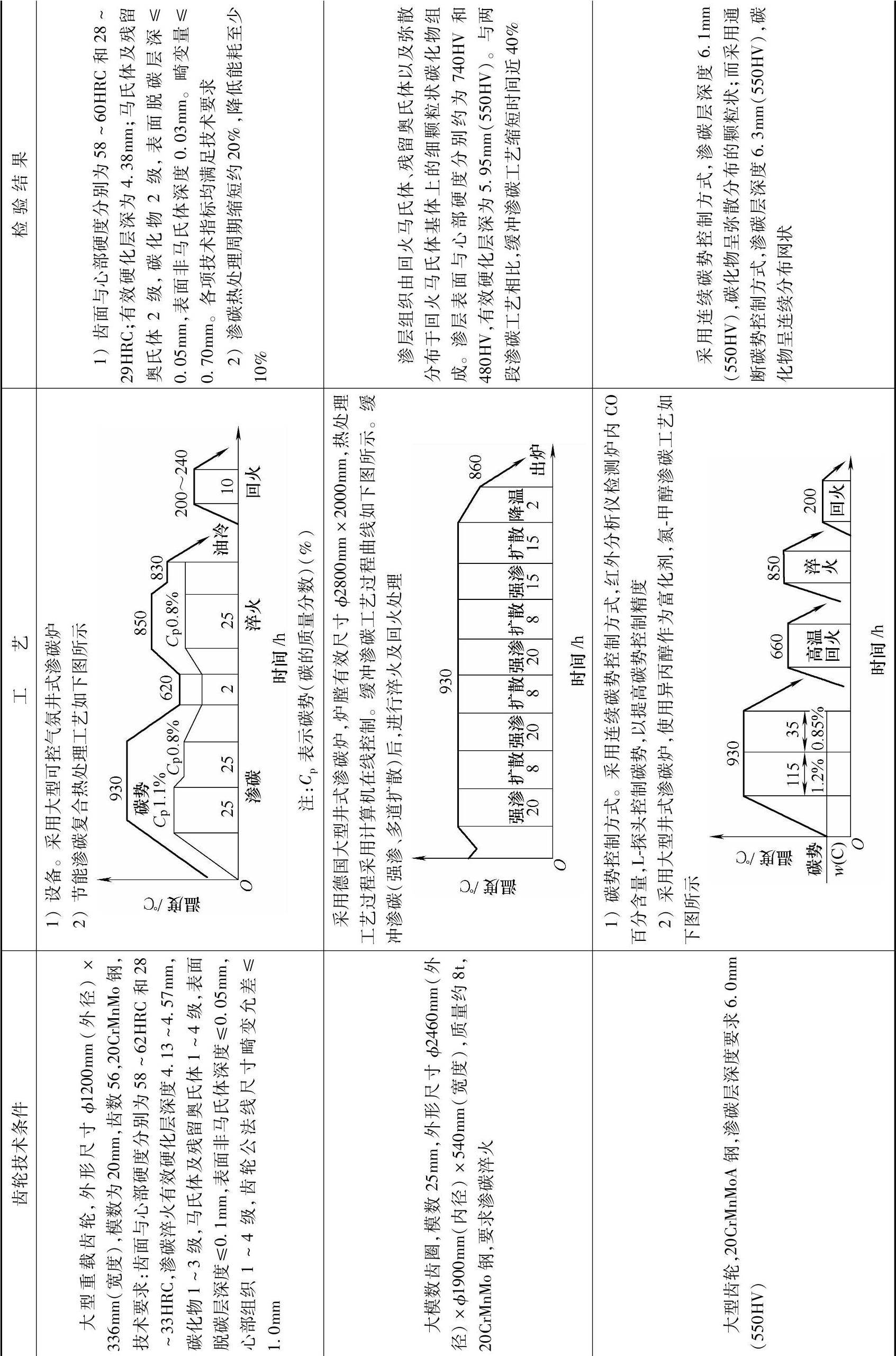
相关推荐